
Interview with Prof. Dr. Julia C. Arlinghaus
"Even More Effort Has to Be Put Into Developing Open Data Standards and Data Exchange formats"
Prof. Arlinghaus, what will the process manufacturing industry look like in the year 2030 as regards digitalization and automation?
The transition to renewable energies and from linear to circular value creation will have to be brought about in the coming decade. Digitalization and automation are the key to this. Manufacturing facilities are becoming more and more autonomous. This means, for instance, that the continuous interpretation of process data with artificial intelligence will make it possible to prevent previously unpredictable process disruptions and to reduce maintenance expenditures at the same time. This will have a positive impact on productivity as well as process stability and thus on supply chains, too. Decarbonizing manufacturing processes will certainly be the biggest challenge. A step in this direction that all companies will have to take in the next three years at the latest is the establishment of end-to-end carbon footprints. And the German Supply Chain Due Diligence Act will require expanding this to include a sustainability footprint in the very short term.
On which technologies and applications should the process industry capitalize as its digitalization proceeds?
Where do you see the greatest potential? We need power-to-X technologies to manage the transition to renewable energies, which is once again being accelerated politically. Demand-responsiveness of energy demands and temporary storage of energy in chemical resources hold major competitive potential for companies. But companies have to do their homework too: IT systems have to be updated and interfaces have to be harmonized. Standardization, using the so-called asset administration shell, for instance, – in other words, establishing the technical foundations for the digital process, equipment and factory twin – is perhaps the most important task: This standardization permits efficient modularization and data acquisition and is thus the basis for new digital business models, too.
The challenges facing the process manufacturing industry up until 2030 are complex and have to be considered from various viewpoints.
Prof. Dr. Julia C. Arlinghaus
Where do you see the biggest challenges on the road to a Process Manufacturing Industry 4.0?
Even more effort has to be put into developing open data standards and data exchange formats to tap efficiency and sustainability potentials throughout the value chain. In addition to standardizing and harmonizing IT systems, IT security will become the main activity. The challenge here is more than just establishing new technologies and software tools. The procedures and processes in companies and throughout supply chains also have to be adapted accordingly. This requires employee involvement at every level and in every area. Lifelong learning must actually be practiced.
What would help overcome these challenges?
The challenges facing the process manufacturing industry up until 2030 are complex and have to be considered from various viewpoints. We must thoroughly gear education and training toward interdisciplinarity and this also means we must invest in education and training just as much as in technology as such. We just completed a study of risks in smart manufacturing, the biggest risk being the human factor – people who do not know how to use technologies correctly or who flat out reject changes. Meeting the challenge of full standardization requires cross-industry and cross-organizational standardization initiatives. Here too, we have to think outside the box and in terms of value networks instead of industries.
To what extent is digitalization helping make the process manufacturing industry more sustainable?
Digitalization establishes transparency. It creates better process understanding and thus facilitates the optimization of processes and the reduction of resource consumption – not only in one company but in the entire value network. Digitalization can also resolve the seeming contradiction between efficiency, flexibility and sustainability. Future manufacturing facilities will be modular. That means they will be scalable and thus easily adaptable to changing conditions. This also pertains to their transformation toward the use of new raw materials just as much as renewable energies.
The Fraunhofer IFF sees itself as a technology and research partner for companies that want to make Industry 4.0 a reality and help shape the epochal transition to digitalization and automation.
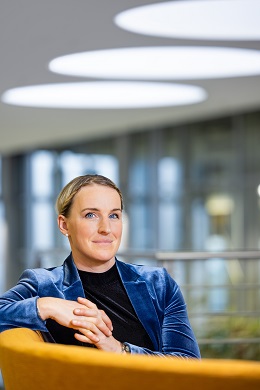
Prof. Julia C. Arlinghaus has been Director of the Fraunhofer Institute for Factory Operation and Automation IFF in Magdeburg since 2019. She is also Chair of the Department of Production Systems and Automation at Otto von Guericke University Magdeburg.