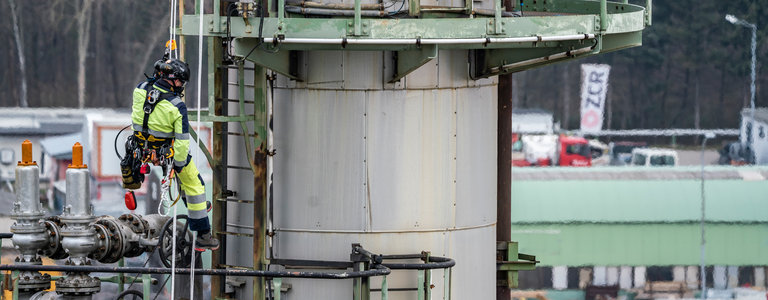
Inspections: From individual solutions to an integrated concept
To ensure that industrial plants can be operated efficiently, safely and with high levels of performance, regular technical inspections are essential in every phase of a plant‘s life cycle. However, inspections can be expensive – and this is all the more true the more complex the inspection requirements and the more parties are involved.
Regular inspection of structures, pressure systems as well as key components and assemblies are required to ensure the integrity of safety-critical systems and to satisfy legal as well as safety requirements. If defects are found it is essential that these are accurately sized and characterised. The results are used to update a Risk Based Assessment of the asset condition to inform future maintenance strategies and to trigger maintenance or repair orders.
Numerous new inspection methods
In addition to using established non-destructive testing (NDT) methods such as acoustic emission testing, ultra-sonic testing or radiography, so-called advanced non-destructive testing (ANDT) methods are becoming increasingly popular. They include, for example, automated corrosion mapping, phased array weld inspection and real-time radiography. The use of drones and flexible rope access solutions also make inspections in hard-to-reach places possible and are both safer and more cost-effective than traditional methods. In addition, the use of semi and fully-automated systems and robots is increasing. The inspection industry is therefore currently undergoing a very dynamic development. The multitude of different methods, however, also means that service providers are often only focused on certain solutions. This is because the new inspection services in particular require not only the appropriate equipment, but also very specific qualifications, accreditations and competencies. Each method also requires specific site preparations. For the plant operator, this leads to a high level of coordination and administrative effort: Not only does he have to coordinate the different service providers (access, maintenance, inspectors), but he also has to be able to interpret and analyse the inspection results to make decisions quickly and effectively. The result is rising costs for inspection activities.
With BIC, we offer all the necessary services along the entire life cycle of a plant from a single source.
Dr. David Hall
Operations Director – Inspection, Bilfinger Salamis UK
Everything From a Single Source
To counteract this, Bilfinger has developed the Bilfinger Inspection Concept (BIC), based on decades of experience of delivering multi-skilled inspection services. It combines various inspection and support services into an efficient solution with just one interface. “With the BIC, we can offer plant operators all necessary inspections along the entire life cycle of a plant from a single source,” says Dr. David Hall, who is responsible for inspection services at Bilfinger. “We cover a wide range of inspection requirements – from pre-fabrication to routine in-service inspections through to decommissioning and dismantling. The result is a package of fully-integrated inspection services.”
Hall sees the greatest advantages for the customer in the efficiency with which all of the required services can be seamlessly integrated and delivered through a single interface and with access to a network of global experts: “Our approach means that the customer only has one central contact person – and thus a single interface. With our large pool of multi-disciplined, qualified specialists from various fields, we cover almost all requirements. We have the relevant certifications for all relevant inspection activities,” says Hall. “And the best thing is that the BIC is modular, which means that each customer selects only those services from the range that they really need. This allows the customer to optimise not only the performance of their plant, but also their budget for inspections.”
Chemistry: CUI by Rope Access
At Shell Chemie Nederland, Bilfinger carried out inspections for corrosion under insulation (CUI) on more than 2,200 pipe bridges as well as non-destructive testing on about 130 pipelines. Instead of using conventional scaffolding, Bilfinger solved these challenges with the help of a rope access team that covered various areas of expertise. The advantage for the client: Halving of the lead times for the preliminary inspection and cost savings of around 900,000 euros (compared to the use of scaffolding).
Offshore: Use of ANDT Methods
On behalf of Taqa in the UK, Bilfinger provides comprehensive inspection services based on BIC. In particular, advanced non-destructive testing (ANDT) and drone inspection methods are used. Accreditation in accordance with ISO 17020 as well as the deployment of experienced and competent technicians guarantee compliance with the highest quality requirements and safety standards.
Learn more

Contact in case of questions:
Dr. David Hall
Operations Director Inspection
Business Unit Engineering & Maintenance
Bilfinger Salamis UK
Tel. + 44 1224246291
david.hall@bilfinger.com