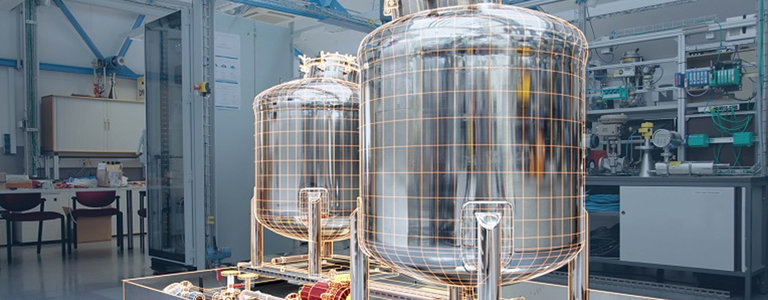
Digital twin: Using integrated data to achieve intelligent control
Digital twins are virtual replicas of existing or not yet developed industrial plants that reflect all of the circumstances, operating conditions and events of the actual plant. This allows for an optimized system design, predictive maintenance, improved industrial asset management as well as a general improvement in the performance of the plant and its systems.
To evaluate or estimate the current status of a plant, the process industry generally relies on historical and statistical analysis methods in addition to regular inspections. This has been the standard approach for years. With the increasing use of digital twins, however, this is about to undergo a fundamental change. Because virtual replication of actual plants means that even complex systems can be monitored and analyzed in near real-time – a development that is now possible with a digital platform that combines and evaluates production and maintenance data. Based on the data, potential defects can be detected even before they occur. It is also possible to identify potential for increasing the efficiency, effectiveness and availability of the plants.
Drawing reliable conclusions on plant performance
“A digital twin renders helpful services throughout the entire lifecycle of a plant,” says Martin Bergmann, Director Product Management & Strategy Development at Bilfinger. “What this means specifically is that unproductive times are minimized, downtimes are eliminated and costs for maintenance and servicing are reduced thanks to intelligent system design. A digital twin also allows for predictive maintenance and optimizes plant and system management.”
From a technical perspective, this virtual plant model is based partly on the Industrial Internet of Things (IIoT) and simulation software, and partly on the broad use of sensors that are used for continuous data collection – including temperature, pressure and flow rate. The digital twin thus experiences the same things as the real plant, but virtually on a computer. “Plant operators can better assess and exploit the possibilities of the plant. In addition, they no longer have to rely on their gut feelings or strict maintenance schedules based on time intervals when they make investment or maintenance decisions. Instead, they can plan necessary conversions or repairs according to actual needs,” says Bergmann.

Contact in case of questions:
Martin Bergmann
Director Product Management &
Strategy Development
Bilfinger Digital Next GmbH
Phone +49 172 9916171
martin.bergmann@bilfinger.com