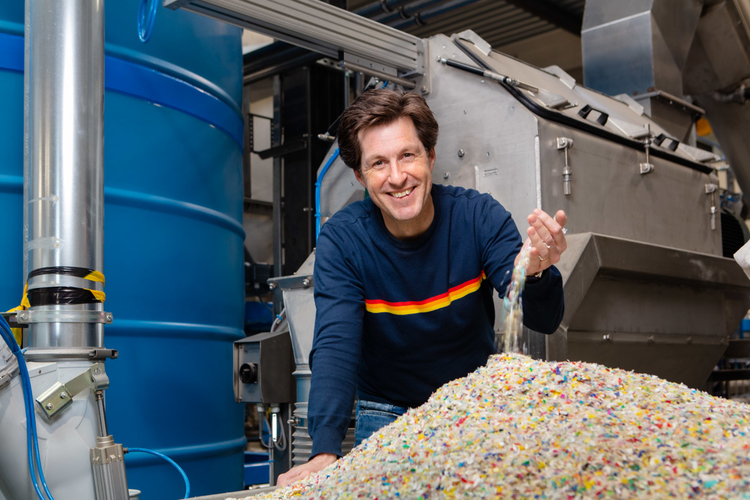
Umincorp: "The most significant recycling effort can be made in plastic"
His motivation? Building a business that expands successfully with innovative technology and good vibes, while making the world a better place. And that is exactly what CEO Jaap Vandehoek does with his company: recycling plastic with the Magnetic Density Separation technology developed by the Delft University of Technology (TU Delft).
As a student Vandehoek joined the Resources & Recycling department at the TU Delft and graduated as a raw materials technologist. A few years later he founded Inashco (Incinerator Ash Company). The company succeeded in refining metal from dry bottom ashes - the residual product that remains after incinerating household waste. The metals can be reused afterwards. In 2013 Vandehoek and his partner Jelle Semee decided to switch to recycling plastic. "That is the area where the biggest steps can be made," is how Vandehoek justifies the switch. "Within the steel production there is already a recycling stream of 60%. Glass, paper and aluminum are also being reused on a significant scale. But plastic still remains. Not least because it is one of the most complex materials to recycle." The main obstacle is that packaging waste consists of various polymers with different densities. Vandehoek explains: "Take for instance a ketchup bottle. Besides the body which is made of a particular polymer, there is the cap on the bottle with a dispensing valve. And on the bottle is a label with an adhesive layer. First you have to thoroughly clean and dry the waste before you can reduce it to clean shreds. Then follows the hardest part: separating by density."
Innovative technology
In order to accomplish that, Umincorp has developed the now patented Magnetic Density Separation technology in collaboration with the TU Delft. "We were looking for a cost-effective method of separating waste plastic in a mechanical way to enter it into a circular circuit. How does it work in simple terms? The cleaned plastic shreds are led to a separation channel. There they are separated into different densities using a ferromagnetic liquid and magnets, which are installed both above and below the channel. Because we achieve an average purity of 97%, at the end of the process the quality we realize is close to that of new plastic. That way, the plastic once more becomes a high-quality raw material and makes collecting plastic more attractive."
The separation channel was first industrially scaled up from a laboratory setting in a pilot plant. "The pilot proved to be very successful, which is why we have now built a factory in Amsterdam." But to be able to really make a difference with the plastic problem and meet international environmental targets, a lot of additional capacity needs to be created. For this reason, Umincorp is currently comparing suitable locations for a second factory.
Circular system
That is where Vandehoek's idealistic principles collide with economic laws. "I am an entrepreneur and need to make some profit. It is therefore important to make it as easy as possible for the major corporations to switch to using more recycled raw materials in their chains. We have to show them that this switch does not have to be more expensive. Especially when you take the environmental damage into account when virgin plastic is simply incinerated after use. Because it is possible to mechanically recycle plastic several times before it becomes unusable. When the quality is no longer satisfactory, you can always chemically recycle the plastic, returning it again to its new condition. That is how you bring about a closed - circular- system. Moreover, the price of virgin plastic - about 1,200 tot 1,400 euro per ton - fluctuates with the price of oil and shows an upward trend over the years. The cost of recycled plastic is constant. In that regard brand owners hold the key. It is high time for companies like Proctor & Gamble, Nestlé and Unilever, as well as for IKEA for example, take responsibility erasing their footprint."
European regulations
Vandehoek believes that while the pressure to recycle plastic is increasing from all directions, it could simply be stepped up. "You notice, for instance, that consumers are more insistent on reducing carbon emissions. However, they have to be willing to choose the possibly paler looking recycled version of their shampoo bottle, instead of the brilliant white one. Additionally European legislation can help considerably. "Currently it is to easy to use virgin plastic. Brussels could for instance introduce an ordinance requiring producers to bring ten percent recycled plastic into the chain. That would be a great start. The percentage should subsequently gradually increase. Furthermore, the chain needs to be more transparent. At present, the number of tons of plastic that go into the recycling units everywhere is being recorded, but not how much new product it produces. And that is because after all the recycled plastic is still being incinerated. I assume the estimates are approximately thirty percent too high."
Meanwhile technological developments continue. "We have been working for several years on a prototype that can separate plastic by color. The next step is to be able to separate plastics by product category or even brand, so that a polymer can be used again in exactly the same packaging."
Collaboration
In early February Umincorp and Bilfinger announced that they will work collectively to build more plastic recycling plants. Bilfinger Tebodin supports the engineering, construction and procurement components for the MDS facilities. They also help with the plant automation and the implementation of the technology. Vandehoek: "Bilfinger is extremely hands-on in the race, they are able to take on large projects and do what is required. They are 'fit for purpose'. In addition, the company is a great sparring partner when it comes to construction, planning, engineering and the desired performance."