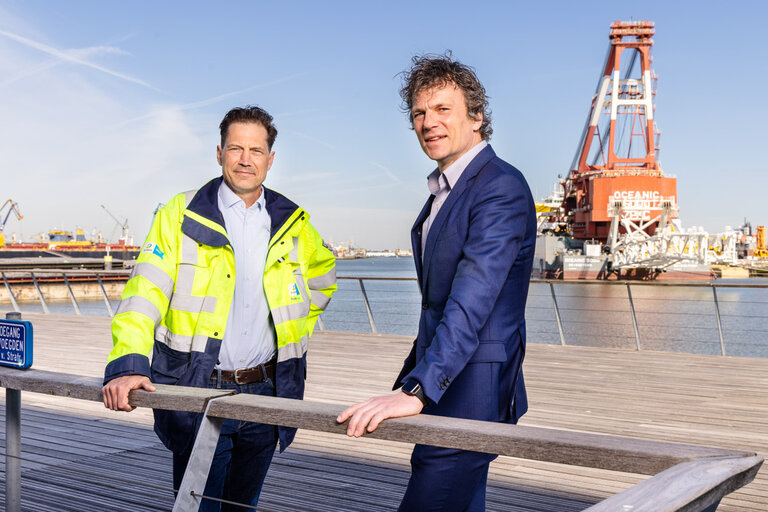
More people are needed in Rotterdam industry
A glaring shortage of workers in industry is a major problem. Not only is it becoming increasingly difficult for companies to get the right people in the right places, even the entire energy and resource transition is being jeopardized. How can we solve this problem? Deltalinqs policy officer Cees Alderliesten and Bilfinger-COO Rob Engelaar give their vision.
Do you want to work in the industry? Then we have a job for you!"
First to the beginning: how did the labor market problem in the industry actually arise? Cees Alderliesten puts it down to a combination of causes: 'First, we have to do with demographics. There are simply fewer young people than before and therefore the labor force is shrinking. A second cause is the prestige of technical professions and "working with your hands" in general. It seems like every parent wants their child to go to college. Well intentioned, no doubt, but disastrous for the prestige of an executive profession. Third, in the urbanized area in and around Rotterdam, I see a strong focus on occupations "in the office" in the economic-legal sphere. Moreover, the port and industry have disappeared from the cityscape in recent decades, and unknown makes unloved.'
Competition
Rob Engelaar does recognize these developments. 'Over the past fifteen years, it has become increasingly difficult for us to find good Dutch skilled workers. That's why we started using skilled workers from abroad back then. But as of about 2015, that has become more difficult. With the accession to the EU, prosperity in Poland and other Central European countries increased significantly. Therefore, there is less incentive to work outside the home country. Or they go to Germany or Scandinavia, where pay is higher than in Belgium or the Netherlands. We have to compete with the whole of Western Europe in our struggle for well-qualified professionals. That forces us slowly but surely to move further and further into countries like Ukraine or Moldova to find new skilled workers. But you do run into complicated regulations if you want to let people from outside the EU work here.'
Dutch influx
Lately, then, Bilfinger has been focusing on increasing its Dutch intake. And Deltalinqs is helping with that. Cees: 'We have various initiatives to that end. Think of the Process and Maintenance College, where young people can follow a training including a guaranteed job. We also organize introductory days for candidates from the "card boxes" of the municipality. People who do not have a job and might be able to work in the industry. So far, to be honest, this has not been a resounding success. But then I immediately put a self-critical note: perhaps we as an industry should also accept that such a candidate will not immediately meet all our requirements and wishes. But with good guidance and "training on the job" or a company school you can come a long way. As long as we are willing to accept that someone then largely does meet and then put him or her in the right place.'
Solving it together
Another critical note Cees places relates to the will to solve this problem together. In the labor market, there is still too much every man for himself. For example, if Bilfinger has recruited and trained someone, it should not be the case that he is snatched away by Bilfinger's customer or competitor with a slightly higher salary offer. We need to make it our responsibility industry-wide that we have enough employees. We also need to become more inclusive. And above all, we have to make it clear: if you want to work in the industry, we always have a job for you! Next, engaging and binding good skilled workers is very important, Rob believes. 'Bilfinger has responded to this by continuously training and retraining employees on their professional skills through its Skills Center. An investment that immediately pays off in both professional competence and commitment.
Image of industry
Another solution is that the image of the industry improves find Cees en Rob. ‘Apparently it is not attractive enough to work in our sector at the moment. In addition, many young people see the industry as “the big polluter”. We don’t have to deny that a very large part of CO2 emissions is cause by industry. But it is also crystal clear that industry wants and must get rid of it. That is why the appeal to critical young people could be: come and help us become climate neutral! In addition, we have to show more clearly that it is really fun and interesting to work in the industry.’
Code black
The shortage on the labor market will be an inhibiting factor in the energy and raw materials transition that we want to make. That is bad news, and the industry is coming off badly in the government’s attention to this. Cees and Rob expect more from the government in this respect. ‘Deploy the scarce people where you can make the most impact, is our call. And that is not just putting solar panels on people’s homes. It is better to use them to help halve a factory’s CO2 emissions. Due to covid-19, the inflow into healthcare has improved, because we suddenly realized how important this sector is. But for an even bigger problem, the climate problem, there is also a threat of code black. And we will only achieve the climate goals if there is also sufficient staff.’
Bilfinger Skills Center
How do we keep or get the craftsmanship of all (new) colleagues and subcontractors structurally on a high level? The answer to that question: with the Bilfinger Skills Center. You can see this as one center with three locations. There is a location in Roosendaal, in Zwijndrecht (B) and in Bergschenhoek. Bilfinger takes case of the onboarding of new employees at each location. In addition, Bilfinger assesses the craftsmanship and safety awareness of subcontractors here and we offer training. You can see the Skills Center as a house that rests on a number of pillars, all of which are related to testing and quality improvement. The first pillar is measurement. The second pillar is making an inventory of what people master and where knowledge and skills are lacking, and the train them accordingly. A third pillar is continuous learning. We do this by offering structured training, education and toolboxes, supplemented with e-learnings. Finally, we also conduct field checks, during which we check on site whether the knowledge is being applied correctly. All content has been compiled in close collaboration with educational and government agencies. This is how we boost the skills of our people.