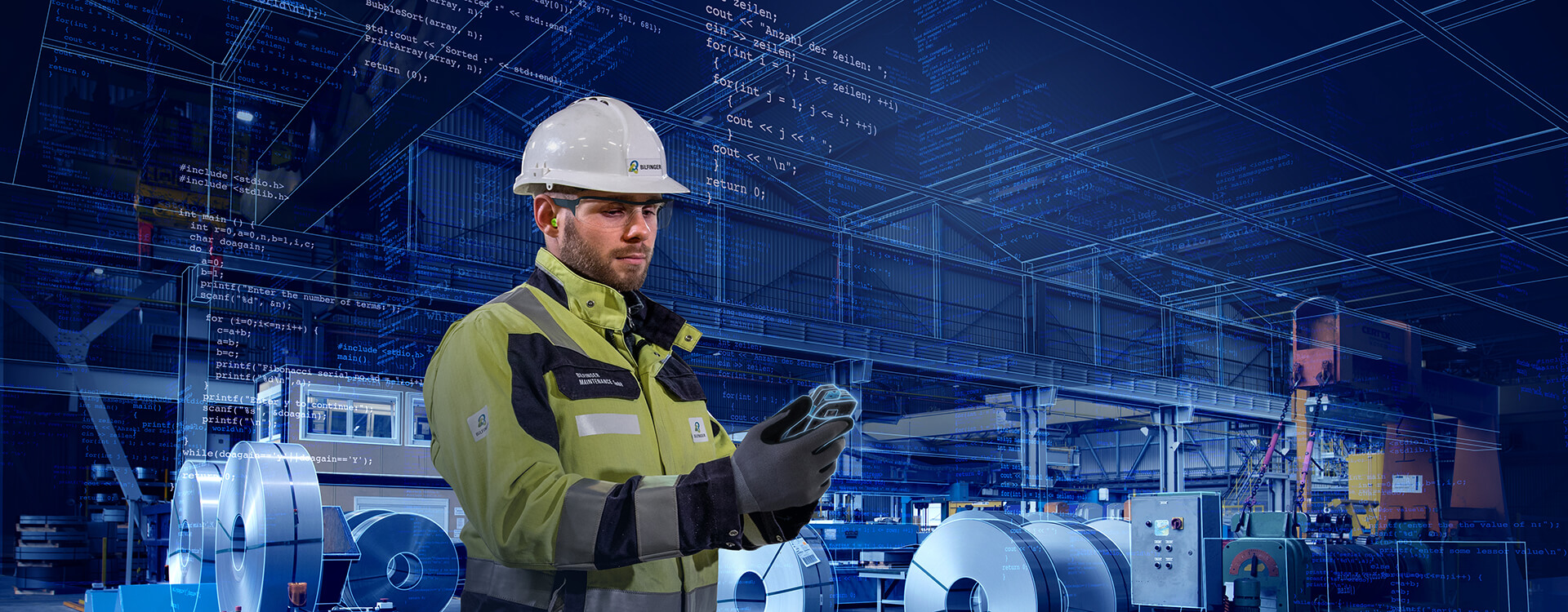
Digital
Digital Solutions for Efficient Industrial Processes and Sustainable Value Creation
By applying innovative solutions, we are making our customers fit for the digital future. We support them in the digital transformation of their work processes, develop intelligent systems for data collection and analysis, reduce costs through the implementation of digital systems and increase the efficiency of their plants.
Digital technologies not only increase productivity, they also generate new data-driven business models. For this reason alone, operators of industrial plants definitely need to take a close look at forward-looking digital applications and solutions so that they can secure their competitive position in the future."
Bilfinger Collaboration & App Platform (BCAP): Your Digital Foundation for Smart Industrial Applications
The integration of various data sources from IT (Information Technology), OT (Operational Technology) and engineering into one platform enables a new way of contextualizing data and information. A deep understanding of the process industry combined with software expertise and data science allows us to discover interdependencies in the data and make them assessable for various applications and stakeholders. Bilfinger Collaboration & App Platform (BCAP) is a cloud-based platform that turns data into value by enabling data migration, process optimization, and predictive analytics.
BCAP is the basis to combine massive data pools in one place. This increases data integrity and quality, improves efficiency in handling data, and allows everyone to access the information. With individual applications and standard solutions in BCAP, we help our customers identify optimisation potential and increase overall equipment efficiency (OEE). This is achieved by reducing quality deviations, improving plant availability and optimising energy costs.
BCAP platform has been specially developed to ease the digital transformation of the process industry. On the one hand, BCAP offers a friendly and simple interface. On the other hand, it empowers our customers to benefit from advanced data analytics, scalability and latest IT security standards."
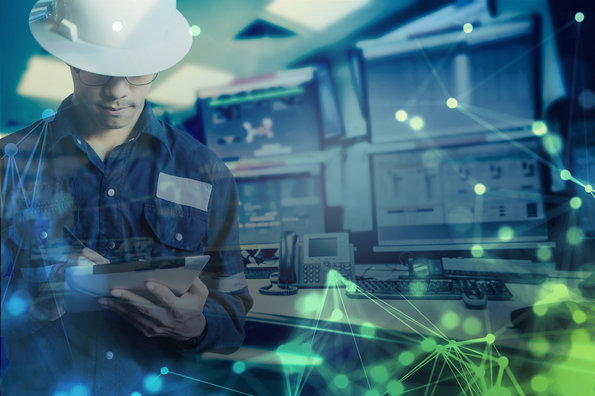
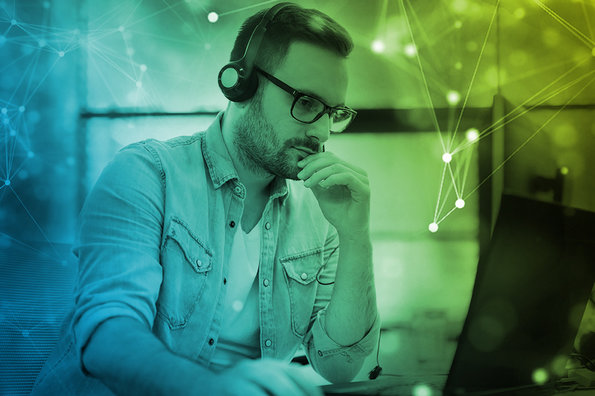
Why Bilfinger Collaboration & App Platform?
- BCAP combines our know-how in maintenance and production in the process industry with comprehensive data science knowledge.
- Once the data is integrated into one platform, various digital solutions can be applied and scaled.
- The BCAP user interface is designed to easily give access to information - from higher management to blue collar employees.
- The role-based setup provides quick insights relevant to each user.
- Data-based decision making reduces costs, improves quality, and boosts the overall equipment effectiveness (OEE).
How BCAP Solutions Deliver Data-Based Value:
- Predictive Quality reveals new insights and improvement opportunities for quality parameters by linking relevant data and applying a virtual sensor or recommender model in the analysis.
- Asset Monitoring analyses and visualizes all sensor data in one dashboard.
- Smart Alerting prevents maintenance and production from alert floods and lets users benefit from artificial intelligence even if they do not have any knowledge of data science.
- The Cognitive Sensor detects voice-related machine modes to reduce maintenance efforts and downtime.
- Plant Intelligence provides a single version of truth and analysis on a plant’s operational performance, availability, and quality.
- BCAP is a scalable platform hosted in Microsoft Azure Data Centers, which are audited for compliance with ISO27001 and ISO27018 standards on an annual basis.
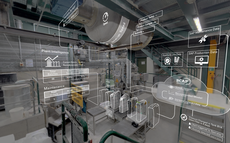
Enhancing Efficiency With Digital Apps – From Practical Experience for Practical Use
Our employees are on site at our customers' plants every day. It is not uncommon for their equipment to include a mobile device that is suitable for industrial use, including special explosion-proof smartphones or tablets. Apps developed in-house by Bilfinger increase the efficiency of work processes, reduce errors during data entry and transmission and provide a high level of transparency. Depending on the workplace and availability, the apps can be used on a mobile device or on a computer as a web app.
Our digital apps include:
Recording and reporting occupational safety-related incidents to prevent accidents and document suggestions for improvement. HSEQ stands for Health, Safety, Environment, Quality.
Documentation and bundling of all information related to a scaffolding project so that the progress of the work can be digitally viewed.
Recording the project progress of shutdowns and turnarounds in order to optimally coordinate individual work steps and to ensure it is possible to react immediately to any potential deviations. In this way, the duration of plant downtime can be reduced.
The Bilfinger Work app is a component of the Bilfinger Maintenance Solution (BMS). It bundels all essential job information for operational employees, such as job assignments, rush orders, materials, and risk assessments.
The Bilfinger Schedule app is a tool designed for SAP-integrated scheduling, facilitating proactive work planning. It enables planners to assign tasks to specific employees, who can then execute these tasks while on the move. This functionality provides planners with real-time visibility into the progress of planned work. Additionally, the Bilfinger Schedule app is part of the Bilfinger Maintenance Solution (BMS), enhancing its capabilities within the broader maintenance framework.
The Bilfinger Check app enables paperless processing of checklists of all kinds. A particular focus here is on equipment subject to mandatory inspection. As we provide many inspection services for our customers, we work with them via the BCAP platform. The Bilfinger Check app is seamlessly integrated into this platform.
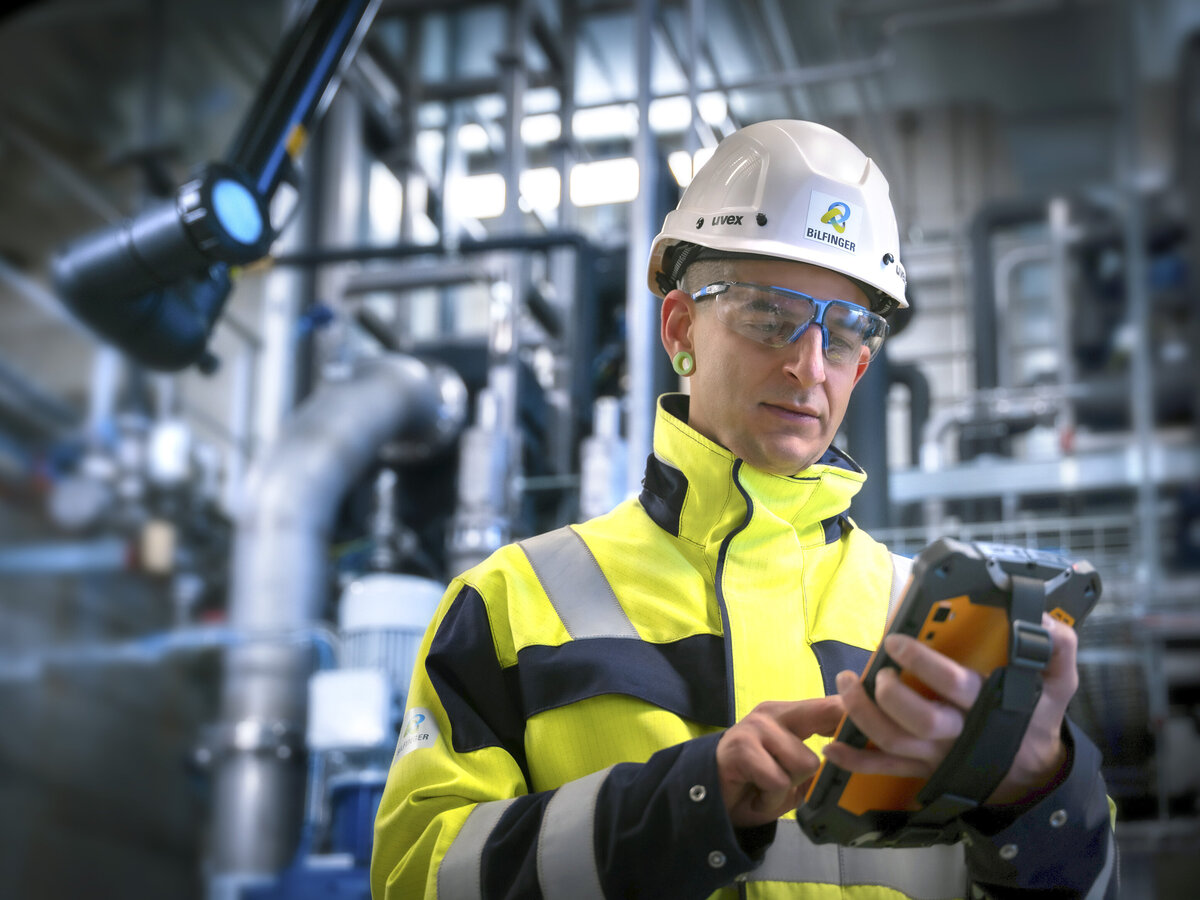
Where Our Digital Expertise Makes a Difference:
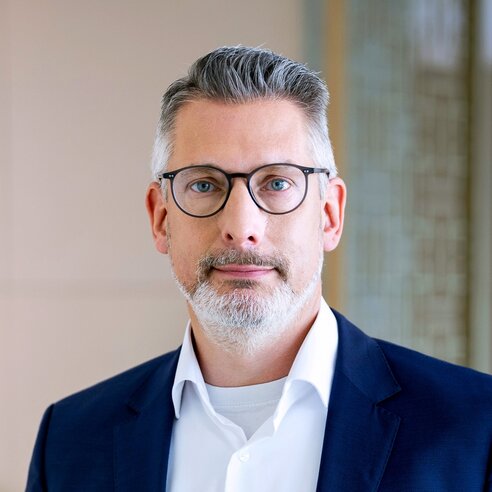
Get in Touch
Global Product Manager Digital