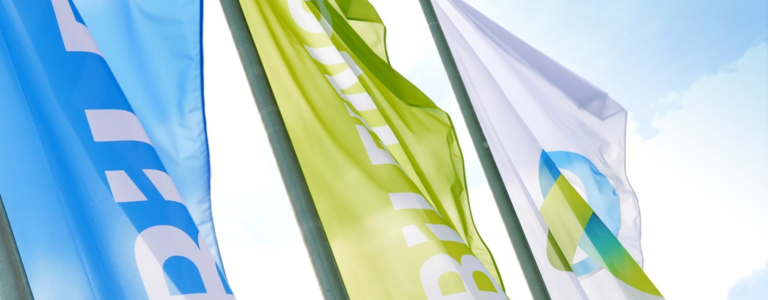
Bilfinger Magazine

Snellere elektrificatie van de industrie
Elektrificatie kan een belangrijke bijdrage leveren aan een klimaatneutrale industrie. Sommige technologieën, zoals de warmtepomp en de stoomboiler, worden al toegepast. Andere technologieën zitten nog in een experimentele fase. Maar het is niet genoeg als een technologie er in het laboratorium veelbelovend uitziet. Het moet zich echt op grotere schaal bewijzen voordat bedrijven het zullen inpassen in hun bestaande processen. Daarom wordt momenteel een operationele testomgeving opgebouwd in het Fieldlab Industrial Electrification.
Het Fieldlab Industrial Electrification (FLIE) is opgericht om veelbelovende innovaties door te ontwikkelen naar bewezen technologie op industriële schaal. Daarmee wil het FLIE de energietransitie in het Rotterdamse havengebied op een praktische manier ondersteunen. Naast de testomgeving helpt het FLIE de industrie met bijvoorbeeld haalbaarheidsstudies, workshops, het ondersteunen van subsidieaanvragen en advies op het gebied van wet- en regelgeving. Het FLIE maakte al succesvolle matches tussen technologieleveranciers en partijen als Shell en Ducor. Daarbij ging het om opslag en hergebruik van restwarmte.
Testomgeving
Maar een Fieldlab is niet compleet zonder een echte testomgeving en die komt er nu aan. Plaatsvervangend Directeur Peter van Hooft legt uit: ‘De industrie wil zeker meegaan met de energietransitie, maar er moet ook geld verdiend worden. Je kunt niet de fabriek een jaar stil leggen om te gaan innoveren. Met een testomgeving op industriële schaal hoeft dat ook niet: wij bieden een plek waar de industrie risicoloos kan testen. Onze pilothal staat op het terrein van Plant One Rotterdam. Het is een ideale locatie: er werken mensen die de procesindustrie van binnenuit kennen, er is hier de juiste infrastructuur en er is een overkoepelende vergunning.’ Het FLIE is een initiatief van oprichters Deltalinqs, FME, InnovationQuarter, Havenbedrijf Rotterdam en TNO. Van de dertien mensen die er werken zijn er twee fulltimeaan de slag: directeur Josepha van Kollenburg en office manager Marga van der Aart. De rest van het team bestaat uit business developers, projectmanagers, een communicatiemanager en een controller, die vanuit hun eigen organisatie de ruimte krijgen om zich aan het FLIE te wijden. Peter vervolgt: ‘Plant One Rotterdam en FLIE delen dezelfde ambities en de kennis, kunde en het netwerk vullen elkaar goed aan.’
Drie productielijnen
In de hal komen in de komende maanden drie verschillende productielijnen te staan. Peter: ‘We hebben deze drie lijnen gekozen op basis van de vraag vanuit de industrie. De eerste is een power-to-heat-lijn. Daarbij gaat het om slim hergebruik van restwarmte of stoom. We bootsen een industriële omgeving na en koppelen daaraan bijvoorbeeld een apparaat dat warmte kan opslaan. Of een apparaat dat stoom kan afgeven aan een opslagsysteem of het kan omzetten naar elektriciteit. In de tweede productielijn gaan we werken aan indirecte conversie van CO2. We beginnen met het maken van waterstof uit water via elektrolyse. We brengen dat samen met CO2 uit de lucht naar een conversie-unit. Hierin wordt de CO2 omgezet in andere chemische bouwstenen, bijvoorbeeld dimethylether (DME), methanol of ethanol. De 100 kW elektrolyzer die we hier neerzetten heeft al een behoorlijke schaal. De conversie eenheid is tien meter hoog; de opstellingen zijn qua omvang en daarmee procestechnologische uitdagingen echt een stap dichter bij de uiteindelijke toepassing in de industrie. Daarnaast is de meeste apparatuur ook mobiel, zodat een validatie op locatie ook mogelijk is.’ In de derde productielijn gaat het om directe conversie van CO2. ‘Hier maken we via een elektrochemisch proces uit CO2 andere chemische bouwstenen zoals CO, formaldehyde, mierenzuur of ethyleen’, vertelt Peter. ‘Deze technologie is nu nog minder ver dan de voorgaande twee, maar gaat er zeker komen. Verschillende partijen hebben delen van de technologie beschikbaar en willen graag duurtesten doen. Over vijf tot tien jaar zullen we hiervan de vruchten plukken.’
Deuren open
De deuren van het FLIE staan wagenwijd open voor industriële bedrijven die willen elektrificeren maar nog niet weten wat voor hun de beste oplossing is, of nieuwe technologie op industriële schaal willen testen. ‘Kom vooral met ons praten’, is Peters oproep. ‘Geef aan waar je uitdagingen zitten en wij kunnen helpen om goede oplossingen te selecteren voor jouw specifieke processen en reststromen. De klimaatopgave is groot, maar te doen. Ik zou graag zien dat de industrie zich in groten getalen bij ons meldt en samen met het FLIE laat zien: we kúnnen dit met elkaar!’
De vergezichten voor elektrificatie van de industrie zijn heel interessant, maar de praktijk van nu misschien nog wel interessanter. Want hoe werken bedrijven in België en Nederland vandaag al aan elektrificatie? Daarvan kan Izak Boot, Lead Engineer Energie bij Bilfinger Tebodin, een aantal concrete voorbeelden geven.
‘Ten eerste moet je niet vergeten dat er nog heel wat potentie zit in efficiënter omgaan met je energie’, zegt Izak. ‘Maar dat ligt bij veel industriële bedrijven ingewikkeld. De restwarmte die bij sommige procesonderdelen vrijkomt, zou je graag willen gebruiken, maar vaak kun je er moeilijk bij of loont het simpelweg niet genoeg. De terugverdientijd is dan te lang om het rendabel te maken volgens de huidige normen. Zonde, want volgens mij laten we hiermee echt een grote kans liggen in de industrie. Door een iets hogere terugverdientijd te accepteren van bijvoorbeeld zeven of acht jaar kan dubbel zoveel energie worden bespaard, met nog steeds een mooi financieel rendement. Slim gebruik van restwarmte en opwaardering hiervan met bijvoorbeeld een warmtepomp is nog steeds een van de meeste kosteneffectieve manieren van CO2 reductie en energiebesparing.’
Elektrische ketel
Een kansrijke optie die veel bedrijven dan wél gebruiken om hun CO2-uitstoot te verminderen, is directe elektrificatie van sommige installatieonderdelen. ‘Een goed voorbeeld daarvan is de inzet van een elektrische boiler voor productie van stoom of heet water. Deze stap wordt vaak gezet vanuit de noodzaak tot CO2-reductie’, weet Izak, ‘want ook hier geldt dat het een kostbare investering is, maar vooral qua operationele kosten vaak een factor 2 tot 3 duurder dan een traditionele gasgestookte ketel. Voordelen zijn natuurlijk dat je CO2-uitstoot bespaart en aangezien de prijs per ton CO2-uitstoot stijgt, wordt de elektrische boiler steeds interessanter. Een ander fenomeen is dat de prijs van elektriciteit schommelt door weersafhankelijke schommelingen in elektriciteitsproductie uit zon en wind. Een hybride ketelhuis kan inspelen op deze schommelingen door de brandstof te kiezen die het goedkoopst is en wanneer de elektriciteitsprijs laag is, de e-boiler te gebruiken.’
Heineken
Momenteel werkt Izak met zijn team aan elektrificatie van de stoomvoorziening van Heineken. Dit bedrijf heeft in een roadmap uiteen gezet hoe ze in 2030 CO2-neutraal willen zijn in alle brouwerijen wereldwijd en vanaf 2040 zelfs in de hele keten. Onderdeel daarvan is het efficiënter maken van de brouwerij in Zoeterwoude, maar dat is niet het enige. Ook de stoomvoorziening wordt duurzamer gemaakt. Een deel van de stoomvoorziening wordt vervangen door warm water, en deze benodigde warmte wordt geproduceerd door warmtepompen. Voor een ander deel gebruikt Heineken nu nog een ketel die deels op aardgas en deels op biogas werkt. Samen met Eneco en Bilfinger Tebodin werkt Heineken nu aan het verduurzamen van de resterende stoomvraag door de plaatsing van een elektrische stoomboiler. De rol van Izak en zijn team is om de e-boiler optimaal te integreren in het productieproces. Eerdere ervaring hiermee deed Izak op in de papierindustrie en stadsverwarming. ‘Voor Heineken zitten we nu in de laatste fase van het ontwerp. In 2023 moet de e-boiler in gebruik zijn en is een belangrijke stap gezet in de vergroening van de brouwerij.’
Niet overal rendabel toepasbaar
Is industriële elektrificatie overal toepasbaar en interessant? ‘Nee. Momenteel is een belangrijke voorwaarde voor succesvolle industriële elektrificatie de aanwezigheid van een grote, zware elektriciteitsaansluiting’, stelt Izak. ‘Want als je dit nog moet laten aanleggen, verhoogt dat de kosten en doorlooptijd fors en is het lastig rendabel te maken. Bovendien vereist toepassing van een e-boiler aandacht voor slimme integratie in het bestaande systeem. Voor lagetemperatuurprocessen zijn er voordeliger toepassingen, bijvoorbeeld integratie van restwarmte of een warmtepomp.’